The photo voltaic panel subcomponent manufacturing market is heating up in the USA. Along with extra backsheets, EVA sheets and glass being made in America, photo voltaic panel makers will quickly be capable to use Made-in-USA junction bins of their ultimate product, because of Amphenol Industrial Operations.
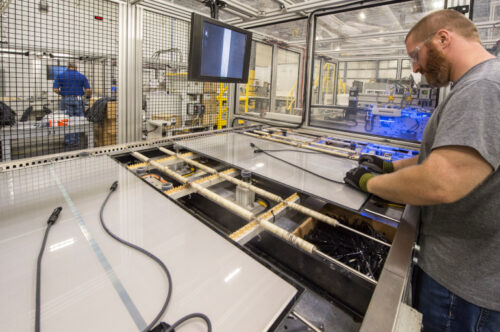
NREL archive picture of junction field and wire meeting on First Photo voltaic Collection 4 modules within the firm’s Ohio manufacturing plant.
Amphenol, one of many world’s largest designers and producers of connectors and sensors, intends to open a 58,000-sq.-ft manufacturing unit in Mesa, Arizona, to make junction bins and their related connectors for each thin-film and silicon photo voltaic panel designs. The ability, which ought to open earlier than the tip of the 12 months, will create 50 specialised jobs within the photo voltaic manufacturing market.
Mark Farrelly, enterprise growth director of environmental options for Amphenol Industrial Operations, advised Photo voltaic Energy World that though Amphenol’s $15 million funding within the junction field manufacturing unit appears small in comparison with the billions being spent on new photo voltaic cell and panel amenities, home junction bins have turn into an necessary a part of manufacturing incentive discussions.
“We had 22 conferences with module producers at RE+, almost all of which expressed larger than 50% curiosity in [Amphenol making junction boxes in the United States],” he mentioned. “They wish to know the way quick, sort of chomping on the bit, asking can we ship this 12 months.”
For photo voltaic panels to qualify for “home content material” bonus credit within the IRA, 40% of their manufactured elements should be American-made. Junction bins are one part that components into the home content material calculation.
Amphenol is a world firm taking part in in lots of industries, principally focusing its photo voltaic enterprise in factories in Shenzhen, China, and Nogales, Mexico. After shortly establishing a junction field meeting web site in Europe final 12 months, Amphenol Industrial feels comfy coming to America.
“Within the final 12 months and a half, even previous to the IRA, there’s been a world motion to diversify exterior of China. Amphenol already had a manufacturing unit operationally in Hungary that had nothing to do with photo voltaic. Considered one of our prospects in Germany requested if we may make junction bins in Europe, so we shortly arrange and did some meeting,” Farrelly mentioned. “Then when the IRA was launched, and the necessity was extra pressing in the USA, it was virtually a no brainer.”
This new Amphenol Industrial manufacturing unit in Mesa joins a couple of buildings within the firm’s army and aerospace operations. Though a brand new constructing with new gear, Farrelly mentioned the startup has been fast as a result of firm’s current presence within the space. A small quantity of product ought to start rolling off traces by the tip of 2023.
Amphenol will deal with two core junction field designs — a rounded unit for thin-film panels and a three-box design for silicon panels. The silicon panel design is pretty generic and simply adoptable throughout most manufacturers — the three-box setup has turn into most typical on half-cell and different superior panel designs. However Amphenol can adapt its traces shortly for customized field designs as wanted.
The junction bins will include Amphenol’s H4 connectors. Farrelly mentioned that he understands the business has defaulted to Staubli MC4 connectors, however the H4 connector was as soon as the dominant model in North America.
“We’re a a lot bigger connector firm, simply not as massive inside photo voltaic,” he mentioned. “I’m hopeful that the junction field enterprise will naturally transfer extra module producers again to the Amphenol H4 household of connectors.”
Junction field manufacturing is measured in items moderately than megawatts. Every line could make 100,000 items a month, and the Mesa facility can have the area for a dozen traces. Farrelly estimates that 1 million junction bins a month is a good evaluation of what Amphenol could make for the U.S. market. (Utilizing a 400-W module as default, Photo voltaic Energy World estimates this to be about 4.8 GW of annual manufacturing.)
“You give me six months lead time, and I’ll construct you as many traces as you need,” Farrelly mentioned. “We now have the demand, we have now the capital to produce as a lot gear as wanted to supply as a lot as they need.”