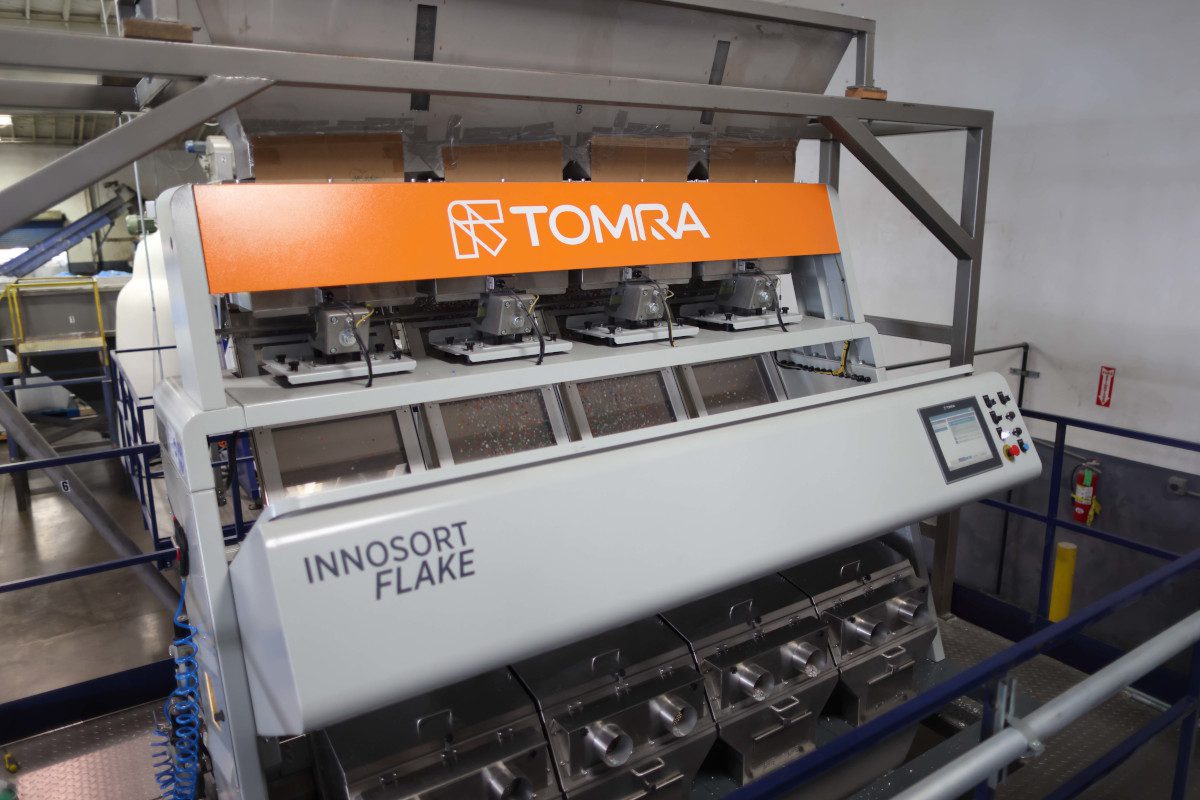
California-based full-service recycler, processor and producer, Greenpath Enterprises, has partnered with TOMRA Recycling Sorting to put in and optimise a plastic flake sorting manufacturing line designed to determine and separate blended polyolefin caps from beverage bottles.
Working for greater than 25 years, the vertically built-in Greenpath accepts a variety of supplies, and the infeed stream is considerably inconsistent. Greenpath creates worth being a one-stop answer by accepting blended infeed hundreds with variable provide streams and producing constant, high quality merchandise.
By way of post-consumer polyolefins – low-density polyethylene (LDPE), high-density polyethylene (HDPE) and polypropylene (PP) – Greenpath accepts movie, inflexible plastics and bottle caps.
“Polypropylene and polyethylene (PE) are collectively probably the most considerable plastic household on earth, however the blended polyolefin market is proscribed for priceless purposes,” feedback Eric Olsson, space phase supervisor, plastics for TOMRA.
PE and PP have very shut density traits and are difficult to separate. So, blended polyolefins are primarily downcycled into extra forgiving purposes that enable for extra contamination.
The hunt for cap to cap
A extra mature PET recycling infrastructure has led to model homeowners incorporating as much as 100% post-consumer recycled content material (PCR) materials of their bottles. As laws tighten to extend the share of recycled content material, the following logical container part to handle is the cap. “We’re on the genesis of making a sorting system for caps that’s related to what’s extra frequent in the present day for bottles. Following Greenpath’s method, the trade can transfer towards a 100% PCR by weight bundle utilizing solely a mechanical sortation,” says Olsson.
Greenpath has in depth processing capabilities with completely different traces to kind numerous feedstock and is adept at mechanical, multi-material and batch recycling processes. To shut the loop on caps, Greenpath investigated numerous applied sciences to kind the blended polyolefins. With PE and PP densities being very shut to 1 one other, float/sink tanks weren’t deemed efficient, and different recycling applied sciences didn’t provide the specified restoration for each PE and PP resins. “The yields are low, and it’s a must to think about the expenditure, area and waste generated from the separation course of,” says Castro.
Greenpath zeroed in on a mechanical answer utilizing flake sorters and met with TOMRA to debate its new INNOSORT FLAKE™ sorting expertise. One among its design parameters was to extract worth from multicomponent plastic waste streams.
“Creating a mechanical sorting course of to shut the loop for food-grade cap-to-cap recycling by persistently separating blended polyolefins by polymer and color with excessive purity is a sport changer,” feedback Joe Castro, president of Greenpath Enterprises, Colton, California.
“It’s finest to pursue a path that introduces the least quantity materials change and types in probably the most environment friendly means, and we haven’t begun to succeed in the ceiling restrict for mechanical polyolefin sorting,” feedback Olsson. “Producing 95% or higher purity-by-polymer streams is vital for a lot of varieties of downstream recycling processes, and flake sorting can get us there.”
Mechanical sorting flexibility
Greenpath’s purity, yield and throughput targets led them to deciding on INNOSORT FLAKE. The unit doesn’t require a big footprint, permitting for simpler integration.
Designed for flexibility, INNOSORT FLAKE incorporates a novel mixture of sensor applied sciences, together with color cameras able to figuring out 16.8 million color variations. “A digital camera is positioned on both sides of the chute, so it may possibly see the distinction between both sides of the flake,” explains Olsson. This helps to determine in-mould labelling that may be a contaminant.
Its FLYING BEAM lighting system gives quick and dependable materials detection by the sorter’s near-infrared (NIR) sensors. Homogeneous gentle distribution ensures classification of PE and PP supplies, in addition to different polymers and supplies. Built-in into the scanner field for cover in opposition to injury, it gives as much as 80% vitality financial savings over standard gentle sensors.
Configuration flexibility permits for single- or multi-step sorting with the identical unit. “We are able to cut up the machine into a number of sorting duties by chute and even cut up a chute into two completely different course of streams or extra,” says Olsson. Castro provides, “TOMRA’s expertise permits us to purify at a better stage that opens up the entire round alternative with going cap to cap,” he says.
Optimising for consistency
Each firms have been dedicated to getting the method proper and have paid particular consideration to sorting optimisation. “We wished an organization who would help us on this journey. TOMRA has been very supportive on this venture. It has been extra like a partnership,” says Castro.
Optimising the method means assembly Greenpath’s excessive purity targets of mono-polymer PE and PP from inconsistent blended polyolefin feedstock. Whereas there’s nonetheless some work to be finished on the facility, “mechanical viability is there,” confirms Olsson.
The system first types by polymer utilizing INNOSORT FLAKE after which by color. “If a buyer desires a pure or particular sorted color PE or PP product, we are able to purify and supply them a sorted color that meets their particular utility utilizing PCR,” says Castro.
TOMRA’s Olsson exhibits optimism for the accomplishment, its influence in the marketplace and what it means for packaging firms attempting to satisfy recycled content material targets. “We’re at first for blended waste streams of polyolefins going closed loop. It gained’t simply be a pipe dream for polyolefins anymore.”