Join every day information updates from CleanTechnica on electronic mail. Or comply with us on Google Information!
As momentum for electrical autos accelerates within the U.S., a talented and educated auto manufacturing workforce can be obligatory for a profitable transition.
Insurance policies just like the Inflation Discount Act and Bipartisan Infrastructure Legislation have helped ship greater than $154 billion in investments into constructing electrical autos and elements. By 2035, EVs might probably account for 71% of U.S. automobile gross sales; and are anticipated to extend to 80% to 100% by 2050. However there are lots of unknowns about how this transition will influence U.S. auto manufacturing staff.
Almost 900,000 staff are accountable for manufacturing giant auto elements or methods and assembling ultimate inside combustion engine autos at authentic tools producers (OEMs) and Tier 1 suppliers, in keeping with knowledge analyzed from the U.S. Bureau of Labor Statistics (BLS). These autos are powered by burning gasoline versus EVs, which depend on electrical motors and battery packs as an alternative of inside combustion engines and elements like fueling and exhaust methods. As elements inside powertrain methods are anticipated to be the supply of the biggest manufacturing variations between the 2 sorts of autos, it’s anticipated that there can be vital implications for these staff.
Key Variations Between Inside Combustion Engine and Electrical Autos
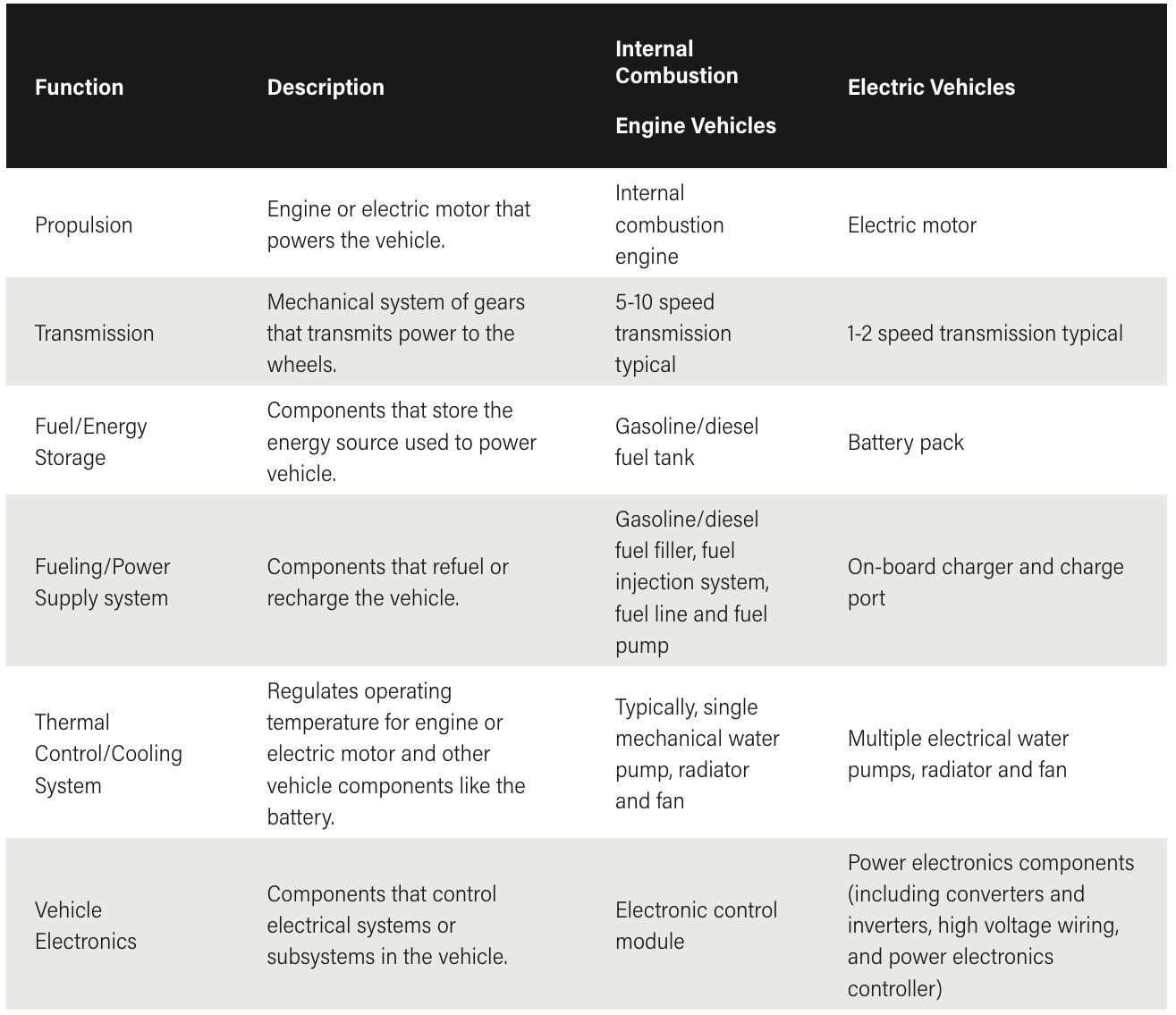
Many questions among the many auto workforce are due to this fact rising:
- What sorts of occupations are anticipated to see disruptions?
- Which new occupations will EVs and their related elements or applied sciences require?
- How will coaching necessities be up to date to make sure that manufacturing staff acquire new expertise?
- The place will in-demand jobs within the EV provide chain be positioned: in legacy auto manufacturing communities or in burgeoning facilities of automotive innovation, just like the Battery Belt?
Listed here are 4 methods the EV transition will influence demand for manufacturing expertise and labor, together with job high quality concerns reminiscent of honest wages, protected work environments and work-life stability. These insights can assist form the insurance policies and methods that drive a home EV provide chain, whereas guaranteeing that auto manufacturing communities — each legacy and new — see the creation of high-quality, community-sustaining jobs.
1) Key Manufacturing Variations Will Remodel Many Auto Business Jobs
Provide chain jobs which are linked to elements solely related to inside combustion engine autos reminiscent of engines and gas injection methods, could have the best danger of displacement as extra EVs are produced. Of the greater than 886,000 staff at OEMs and Tier 1 suppliers — companies that manufacture giant elements or methods and assemble ultimate autos — near 58,000 staff targeted on gasoline engines and engine elements manufacturing are prone to expertise essentially the most extreme employment impacts. Fifty-seven p.c of these staff are positioned in Michigan, Ohio, Indiana, Tennessee and Kentucky.
Alternatively, Tier 1 companies that manufacture non-powertrain elements (like steering, suspension, and different inside elements) which are widespread throughout all types of autos could expertise low or no impacts.
In between, there are some suppliers who’re prone to witness medium disruption and might want to readjust their workforce. For example, the shift in direction of electrification will considerably influence machine device producers. EVs require fewer in addition to completely different powertrain elements, which in flip require completely different machine instruments for manufacturing these elements.
The Biden Administration has already introduced $15.5 billion in investments devoted to retooling manufacturing services, with an emphasis for creating good high quality jobs and supporting services with robust ties to auto manufacturing.
Auto Manufacturing Employment Disruption Dangers In the course of the Transition to Electrical Autos
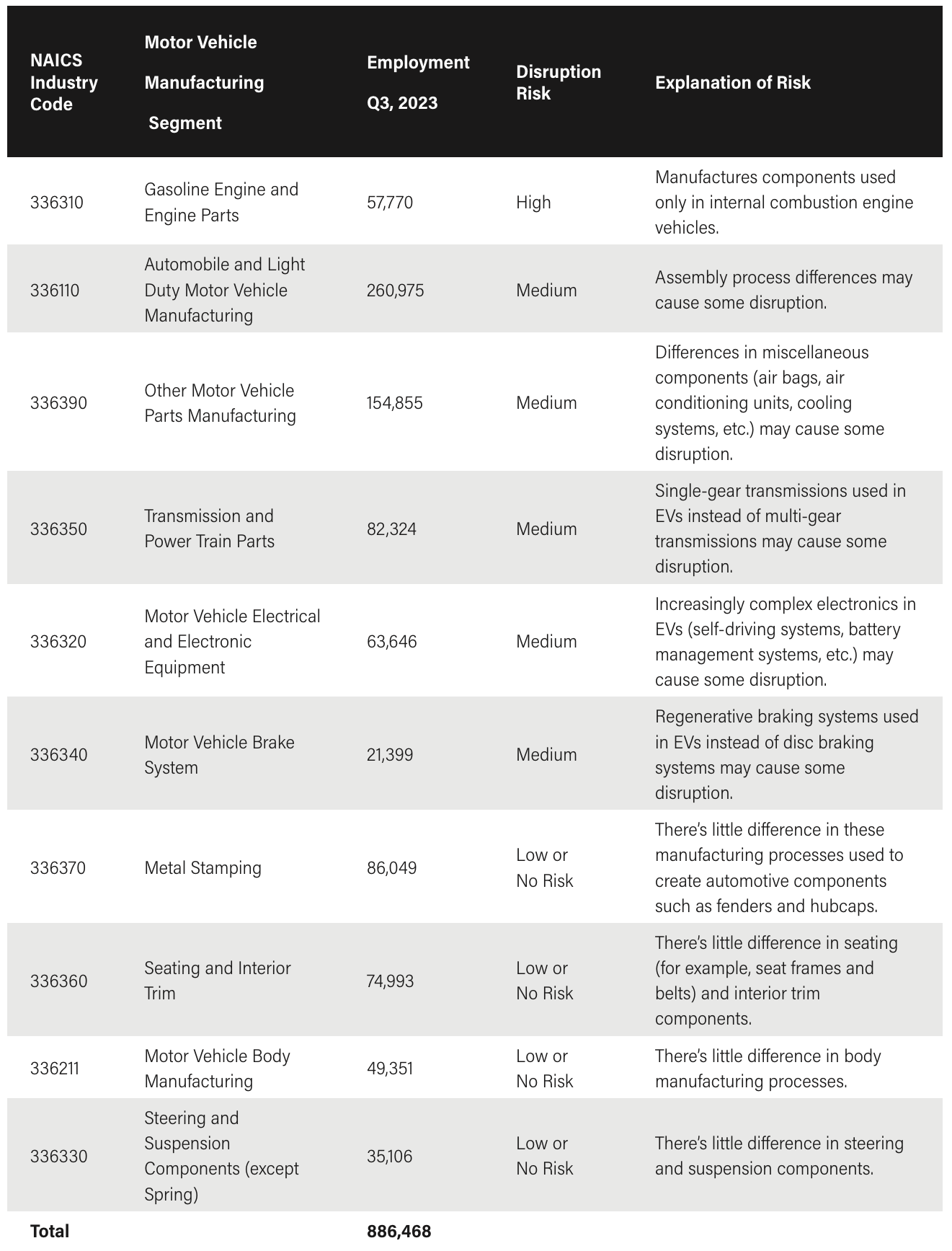
Job disruptions at Tier 2 and Tier 3 companies which are additional down the provision chain (as an illustration, tire manufacturing or paint and coating manufacturing), are additionally prone to be restricted or not see any impacts in any respect, as many of those elements could also be agnostic to how the automobile is powered. These corporations are additionally extra prone to provide different industries past the automotive trade. This might range throughout completely different companies relying on how closely their manufacturing is tied to automobile elements.
As the marketplace for inside combustion engine automobile elements — from fuel tanks to gas injectors — shrinks, suppliers of these elements should select embrace the EV transition and adapt their workforce to new product traces. Small-to-medium sized companies with decrease revenue margins might discover it harder to transform their manufacturing traces for the EV trade or diversify to different sectors than bigger corporations. Moreover, uncertainty about how shortly the rising marketplace for EV elements will overtake inside combustion engine elements may cause companies to be not sure about any workforce adjustments they might want to make. Current developments additionally level in direction of different concerns. For instance, how will hybrid autos match into this new automobile market? Regardless, staff who’re transferred to new merchandise would require retraining.
In the meantime, EVs are prone to generate rising demand for jobs associated to the design and growth of assorted EV fashions, manufacturing of batteries to energy them and charging stations to maintain them operating on the street. As software program and energy electronics use will increase in autos, occupations in pc and engineering fields will play a pivotal position of their design and growth.
Equally, the opening of latest battery manufacturing services will generate vital new jobs. The BLS estimates employment on this trade and different industries related to automobile electrical tools manufacturing to extend by 17% between 2021 and 2031, making it one of many quickest rising manufacturing industries. Presently, the battery manufacturing trade employs 52,500 staff, in keeping with the BLS.  An evaluation by WRI and BW Analysis Partnership estimate that 13,400 of those staff are concerned within the manufacturing of vehicle-related batteries, based mostly on Motor and Tools Affiliation’s  assumption that 27% of employment within the battery manufacturing trade is expounded to the automobile provide chain. Employment in battery manufacturing is poised to extend considerably as a result of investments happening in battery element, cell and pack manufacturing.
Scaling up battery manufacturing will require extra engineers who can design and take a look at batteries in addition to extra assemblers, technicians and different manufacturing staff to function machines and transport supplies safely. A latest employer-focused battery trade workforce wants evaluation carried out by the Heart for Automotive Analysis highlights that employers anticipate hiring to extend by greater than 20% by 2026 with roles like engineering, technician, and producer/assembler in excessive demand.
Moreover, a 2022 examine by researchers at Carnegie Mellon College finds that the labor depth of producing EV powertrains could also be larger than inside combustion engine automobile powertrains as soon as accounting for battery manufacturing. There may be additionally rising recognition that assembly-related labor hours for EVs are larger than for inside combustion engine autos.
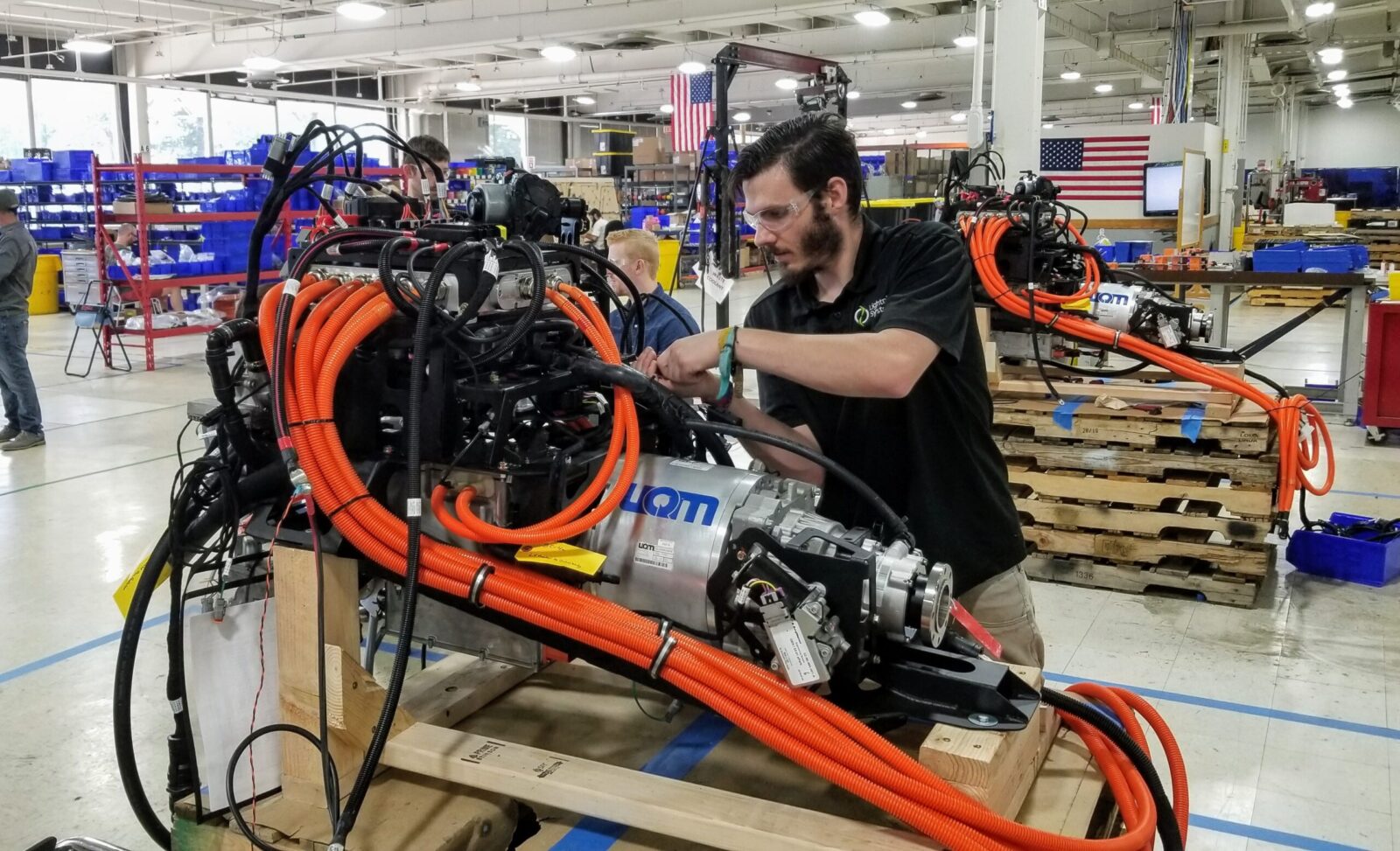
2) The EV Transition Will More and more Require New Digital, Superior Manufacturing and Specialised Abilities
The transition to EVs will shift the auto trade from a very mechanical manufacturing course of to an electrochemical manufacturing course of. These technical calls for imply that staff with technical and digital expertise can be more and more wanted to work together with human-machine interfaces, analyze and handle knowledge, and make the most of specialised data of auto applied sciences and methods pondering. Chemical expertise and safety-focused expertise together with the flexibility to deal with hazardous EV elements or elements are some different noticeable gaps.
Extra particularly, some distinguished talent gaps that downstream employers (for instance, cell and pack manufacturing, automobile functions like meeting or disassembly, and battery recycling) are involved with embrace chemical engineering and supplies science, battery chemistry and competency with battery administration software program methods. Different carefully associated expertise together with testing and high quality management, managing automated instruments and knowledge evaluation for course of management may also be in excessive demand.
Staff’ views additionally level towards the necessity for various coaching concerns. One other Carnegie Mellon College examine, which interviewed manufacturing staff and technicians throughout completely different U.S. auto companies, exhibits that whereas there are overlaps within the vary of expertise required for each EV and inside combustion engine automobile operators and technicians, manufacturing practices utilized by EV producers could enhance the demand for choose expertise like advanced downside fixing and protected chemical dealing with. Cross-cutting expertise and precision and engineering expertise related to electronics and electrical elements are different rising necessities which are prone to enhance.
3) Synthetic Intelligence Vertical Integration Will Probably Impression Staff and Their Wanted Coaching Â
Growing use of synthetic intelligence within the automotive provide chain and vertical integration are already contributing to workforce disruption and are prone to turn out to be a bigger challenge within the EV transition.
Robots and machines are already on the manufacturing facility ground around the globe, with most automotive factories leveraging some extent of automation at almost each stage of auto manufacturing. Now AI is poised to play an even bigger position all through the automotive worth chain because the trade transitions to EVs. Inside automotive manufacturing itself, automakers are starting to make use of AI to streamline the analysis and growth course of for brand spanking new autos, reduce design and growth time, and establish and proper flaws through the manufacturing of the autos. For EVs, AI is getting used to foretell battery upkeep and undertaking its lifespan. This may assist drivers know when they should substitute the battery whereas additionally enabling automobile producers to enhance analysis and growth.
The automotive trade will more and more want staff with AI expertise, machine studying and knowledge evaluation, and can be competing with different industries reminiscent of software program and semiconductor for expertise. AI applied sciences might additionally enhance automation and alternative of sure jobs.
Automakers are additionally vertically integrating by shifting battery and different elements like motors in-house so as to have extra provide chain management and retain mental property. That is an consequence from the various supply-chain disruptions that resulted from the COVID-19 pandemic, a supplies scarcity and climate disruptions. It’s additionally in distinction to many years of follow the place automakers handed management over automobile growth and manufacturing to completely different suppliers who would produce all the things from steering controls to semiconductors and digital elements for a number of automobile producers.
Tesla for instance, has adopted an strategy of sourcing uncooked supplies straight, constructing its personal batteries and engineering its personal software program. As different automakers comply with Tesla, they might want to considerably construct capabilities and in-house experience in battery applied sciences, inverters and electrical powertrains.
On the similar time, vertical integration can probably result in much less enterprise for automotive suppliers.
All these developments work together with each other and can’t be checked out in isolation. Extra importantly, all of them have workforce implications and any subsequent suggestions ought to account for his or her influence on staff and their wanted coaching.
4) Job High quality and Honest Compensation Are Key to Guaranteeing an Equitable and Simply EV Transition
With extra EV manufacturing poised to happen within the U.S., supercharged by insurance policies just like the Inflation Discount Act and the Bipartisan Infrastructure Legislation, there are considerations about job high quality and union negotiating energy.
Jobs within the automotive trade have been as soon as a ticket to the center class, with excessive pay and good advantages. Nonetheless, in the previous couple of many years, U.S. auto staff have witnessed a vital decline in wages, working situations and union bargaining energy. This has been accompanied by foreign-owned automotive corporations organising manufacturing vegetation in Southern states to make the most of cheaper, non-union labor.
Between 2001 and 2022, Michigan noticed a 43% drop in each motorcar elements manufacturing and motor autos manufacturing employment. Throughout the identical time, employment in these two industries in Alabama elevated by nearly 3 occasions, whereas in Kentucky, employment ranges fell by 28% between 2001 and 2011, till rising once more by 59% in 2022. In 2022, these two non-union states accounted for 12% of motorcar and automobile elements manufacturing employment within the nation.
The change to EVs is reinforcing these regional patterns.
Roughly, 50% ($85.6 billion) of introduced non-public EV investments has occurred in simply 5 Southern states  — Georgia, Tennessee, South Carolina, North Carolina and Kentucky — that are additionally what’s generally known as right-to-work states, making it more durable for staff to type unions and collectively discount for higher pay and dealing situations.
Automakers are additionally more and more turning to joint ventures and partnerships, particularly with South Korean corporations for battery manufacturing, which elevate extra questions on long-term job high quality and the method of union negotiation in these vegetation. In 2022, when the EV battery three way partnership facility between GM and South Korean LG Vitality Options opened in Lordstown, Ohio, the beginning hourly wage for staff was $15.50, which was roughly half the highest pay of a GM meeting employee.
The United Auto Staff (UAW) contract negotiations that reached settlement within the fall of 2023 between the union and the Massive Three automakers —GM, Ford and Stellantis — spotlight that reversing the detrimental trajectory is achievable. All three contracts embrace a 25% wage enhance over 4.5 years of the contract, the reinstatement of cost-of-living allowance and a shortening of the variety of years it takes for workers to maneuver to the next pay grade.
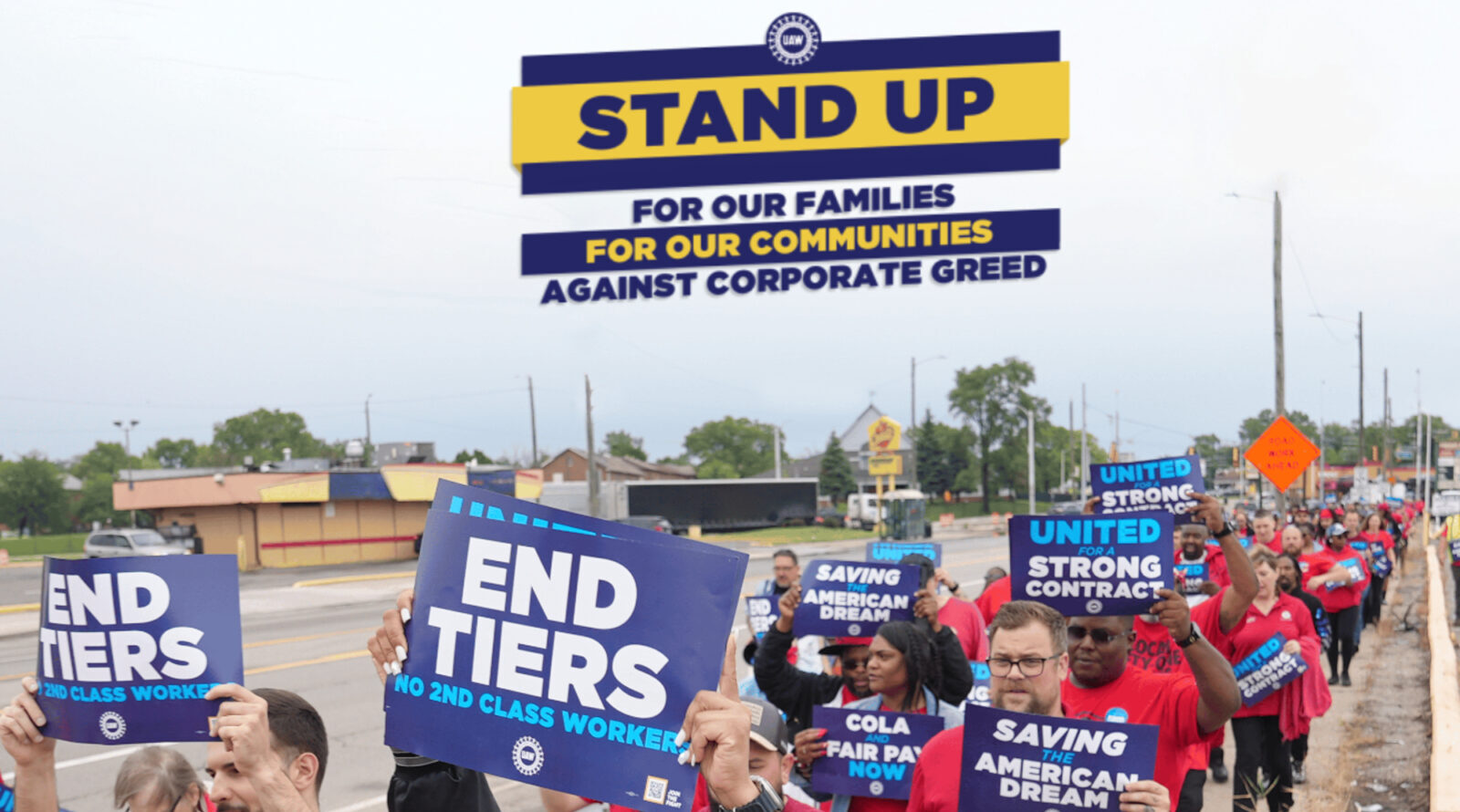
Since then, extra automakers exterior of the Massive Three have introduced raises for his or her staff. Union campaigns are additionally at the moment underway at Mercedes-Benz and Hyundai factories in Alabama, whereas Volkswagen’s Chattanooga, Tennessee plant just lately voted to turn out to be the primary non-Massive Three automotive meeting plant within the South to unionize.
The EV transition underscores that good local weather insurance policies won’t essentially align with good labor insurance policies except a concerted effort is made to make sure that staff and unions have a seat on the desk. UAW’s potential to arrange non-union and international automakers like Tesla and Toyota, particularly in Southern states, can probably enhance job high quality for a broader group of autoworkers whereas additionally guaranteeing a level-playing subject for GM, Ford and Stellantis.
A Expert Workforce Is Essential for the EV Transition
A profitable EV future within the U.S. would require the supply of a talented workforce that capitalizes on current expertise in addition to bolsters staff with new expertise.
The EV transition is an incredible alternative to enhance the prospects for staff and native economies throughout the nation. It can require complete planning and coordination that features all the things from upskilling packages and apprenticeships to internships, college and neighborhood school partnerships and higher outreach to youthful generations. Many stakeholders — together with employers, trainers, workforce program designers and community-based organizations supporting staff and learners — might want to coordinate to keep away from duplicating efforts, establish and handle gaps, and leverage classes discovered from comparable workforce progress in different sectors.
Within the coming months, WRI will proceed its analysis into the EV transition and its influence on staff, together with which new occupations and their related elements can be required, whether or not current auto staff will be capable to switch their expertise to EV manufacturing, and the implications for creating workforce training and coaching packages.
By Devashree Saha, Rajat Shrestha, Nate Hunt, and Evan Kim. Courtesy of WRI.
Have a tip for CleanTechnica? Need to promote? Need to recommend a visitor for our CleanTech Discuss podcast? Contact us right here.
Newest CleanTechnica.TV Movies
CleanTechnica makes use of affiliate hyperlinks. See our coverage right here.