Wind Harvesters use extruded blades produced from plane aluminum. The fiber and resin blades of most wind farm scale HAWTs (horizontal-axis wind generators) use customized molds and a whole lot of expert labor. Extruded blades are a lot inexpensive to fabricate and if made like ours, have a fatigue lifetime of over 70 years and are totally recyclable.
Our Mannequin 3.1 blades wanted reinforcing on the connections to the higher and decrease stage arms to assist alleviate stress concentrations attributable to the bolt gaps. Listed here are some photographs of Omar and Antonio including a exactly crimped aluminum plate to the place the holes are situated, rising the pores and skin thickness and lowering the stress focus on the space the place the blade is linked to the arm. Sanding, acid etching, poisonous epoxy, cautious alignment and exact strain, temperature and humidity have been wanted. After putting in six of those plates, our engineers have been motivated to discover a manner to not use them.
Antonio (left) and Omar (proper) end fixing the primary plate to a blade and can watch for the epoxy to remedy.
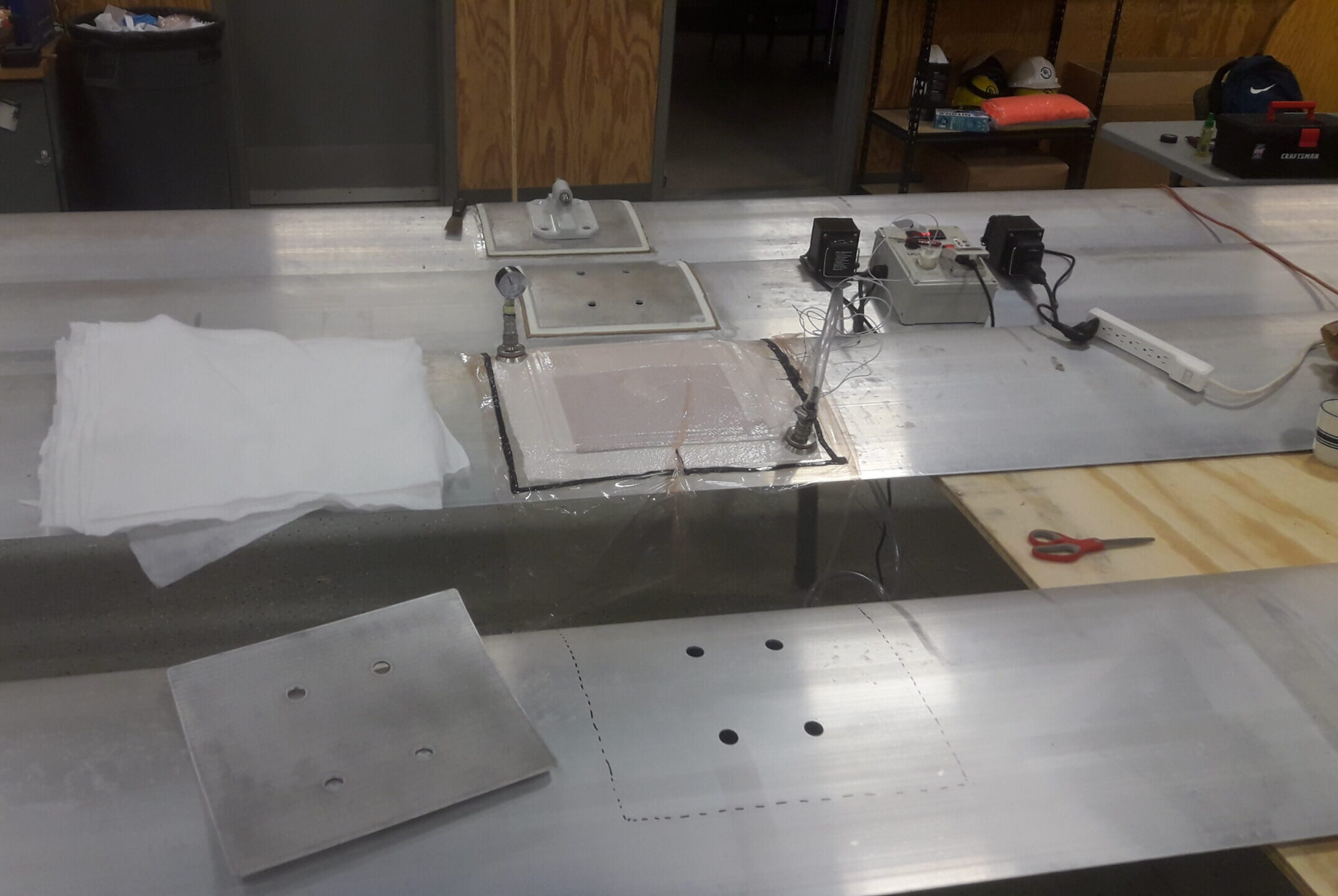
Three plates finished. A fourth prepared for sanding, acid etching and including the epoxy.
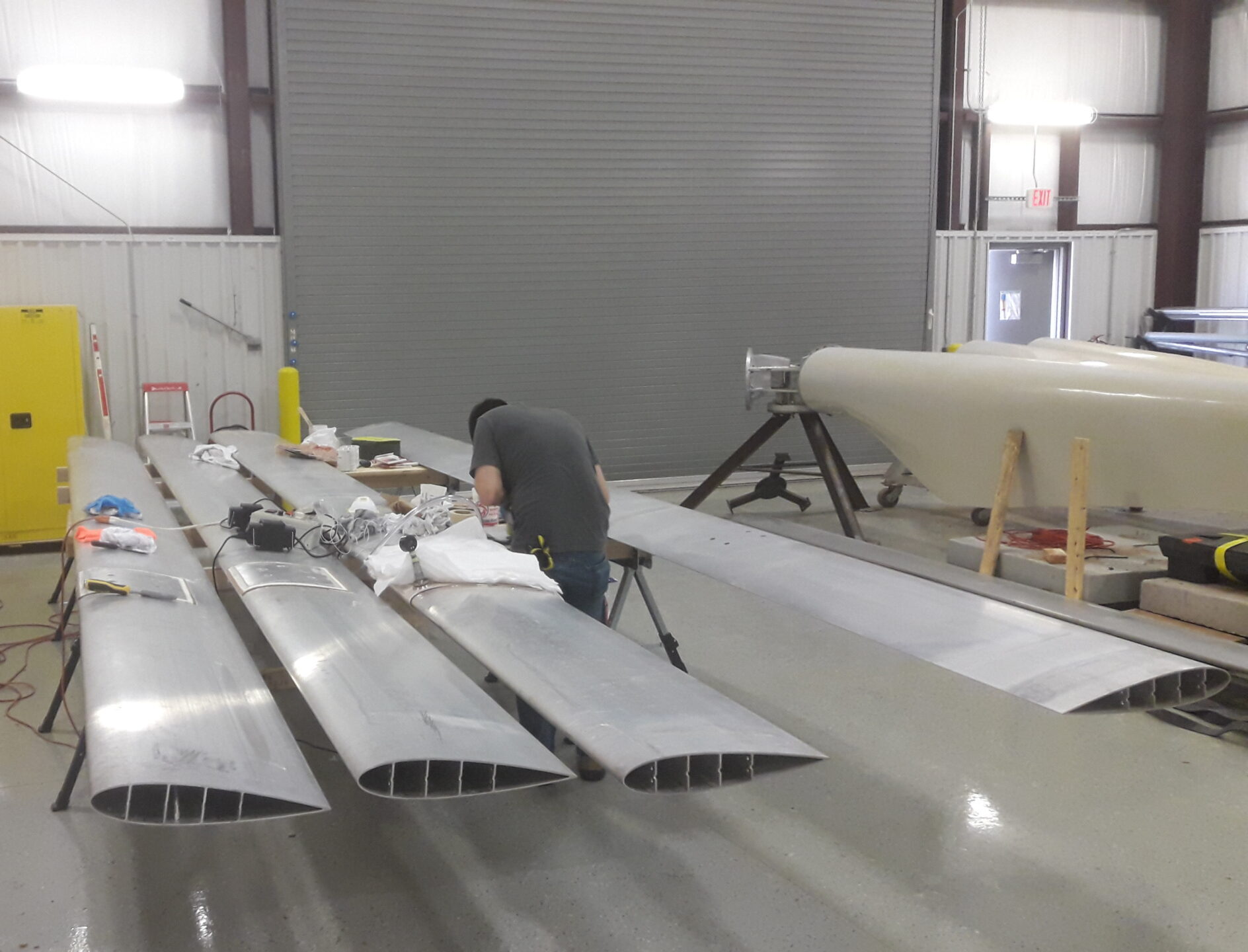
Notice the top of Mannequin 3.1 blades present the uniform width of its pores and skin and inside partitions.
So we employed Iopara Inc to judge three totally different formed blades plus the NACA 0018 blade that we’d used on nearly each turbine since co-founder Bob Thomas (deceased) began designing and testing vertical-axis wind generators. Iopara’s aerodynamic modeling confirmed that an virtually 50% bigger, NACA 0021 formed blade would produce about 3% extra vitality than any of the opposite profiles.
Nutbar exhibiting the personalized curve to match the blade and the threaded gap for the set up rod.
Now, how may we use this larger blade and take away the necessity for the epoxied plates?
Our good engineering workforce found out that some components of the blade may very well be thinner and others thicker with out altering its weight or core power. An extrusion die simply accommodates this variability. The unhealthy information is that others have used variable thick blades, so that’s not patentable. The excellent news is that nobody can stop us from utilizing this.
Final week the US Patent and Trademark Workplace (USPTO) knowledgeable us that there was a part of the variable thick blade concept that nobody had considered earlier than – the interior nutbar bracket. These photographs of the nutbars for Mannequin 3.1 explains why this bracket will get monetary savings and meeting time.
You must look intently to see that Mannequin 3.1’s nutbar is customized made. The aspect that lies towards the blade has to completely match the curve of the blade. Then on the sting, a threaded gap must be fabricated so {that a} rod can transfer the nutbar into place.
The nutbar holes line up with the blade arm bracket bolt holes.
Our “bracket” invention permits for an off-the-shelf nutbar for use as a result of the underside of the bracket is extruded to be flat, not curved. The edges of the bracket information the nutbar in order that one can push it into place with a stick and the threaded rod isn’t wanted. This invention saves a whole lot of {dollars} per turbine in components alone and much more in diminished labor prices.
The variable thick blade concept permits us to eradicate the epoxied plate and customized made nutbars. The elevated masses the bigger blade creates will increase vitality output. The icing on the cake is that this blade breakthrough triggered a slew of extra patents. We are going to share a few of these in future weblog posts. Keep tuned.
Nutbar with rod connected, able to be moved into place 5 ft deep within the blade.
The connection bracket on the plate is bolted to the nutbar that’s pushed 5 ft or so contained in the blade to line up with its bolt holes.