Join every day information updates from CleanTechnica on e-mail. Or observe us on Google Information!
It’s the scale of virtually two basketball courts and consists of 4,400 battery modules: the brand new battery storage system to produce the Porsche Plant Leipzig with energy. The extraordinary factor is that this stationary power storage system was constructed out of used Taycan batteries. They had been taken from precollection and works automobiles and are actually being put to make use of as a stationary power storage system on the finish of their service life.
With the “Second Life” idea, Porsche is demonstrating how used high-voltage batteries from electrical automobiles might be put to good use and preserve sources in a second use part. The challenge concept originated within the Environmental and Vitality Administration unit of the Stuttgart-based sports activities automotive producer.

A round financial system, good power provide and extra
The challenge gives vital insights into how you can provide an automotive plant with power in an clever vogue. It additionally facilitates the enlargement of an adaptable energy grid. “In fact, that is about environmental points and the core situation of the power provide. Nevertheless it was additionally vital to us to take a pioneering position with the storage system,” says Alwin Schmid, Head of Electrical Engineering at Porsche, explaining the targets of the challenge.
Schmid is the initiator of the challenge, which was primarily based on a feasibility examine in collaboration with the College of Utilized Sciences Zwickau. “On this unprecedented mannequin challenge, we had been in a position to mix numerous totally different targets, together with peak load capping, optimisation of self-consumption and simultaneous participation within the power market.” This versatility when it comes to utilization makes the Porsche pilot challenge distinctive within the discipline of business power storage.
From the challenge concept to implementation
“The challenge exemplifies how we are able to use sources sustainably and mix this dedication with enterprise effectivity,” says Albrecht Reimold, Member of the Govt Board for Manufacturing and Logistics at Porsche AG.
“We wished to create electrical energy storage capacities for the Leipzig plant so as to make the positioning much more economical and to extend its diploma of self-sufficiency. So it was solely logical to make use of batteries from Taycan preseries automobiles as an alternative of recycling them,” explains Jonathan Dietrich, general challenge supervisor for battery storage. “We hope to achieve insights from the challenge so as to have the ability to equip different Porsche places with related techniques and capabilities sooner or later. On the similar time, we are able to utilise batteries from take a look at vehicles which can be now not appropriate for demanding use within the automobile for a second helpful deployment earlier than their ultimate recycling.”
“Energy cubes” — the technical construction
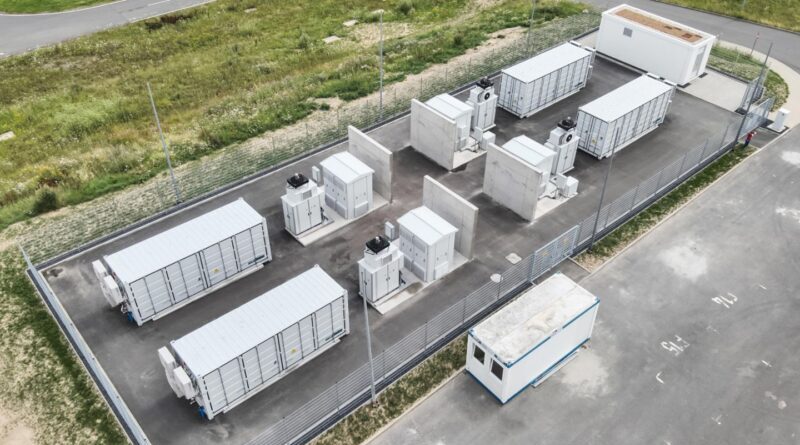
The technical specs of the stationary battery storage system are spectacular: The entire capability is 5 megawatts with an power content material of 10 megawatt-hours. The storage system might be operated at as much as 20 per cent overload for brief durations. It’s made up of 4,400 particular person battery modules, divided into 4 battery containers.
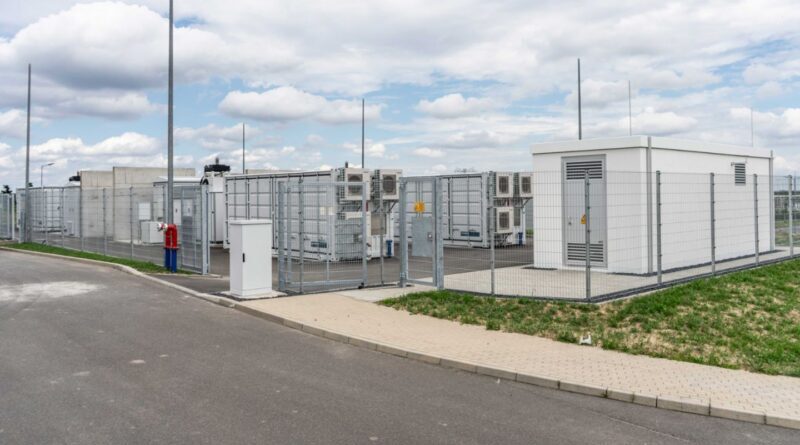
The battery modules used within the gruelling on a regular basis work of take a look at automobiles had been put in within the power storage system with none technical adjustments. The 4 battery strings are every related to an inverter and a transformer in a medium-voltage system. The complete system, together with the battery blocks, is designed for a helpful lifetime of greater than ten years; particular person battery modules might be changed individually if needed.
Energy storage for the plant and a part of the power transition
The electrical energy for the storage system is partly generated by the plant’s personal photo voltaic techniques with a peak output of 9.4 megawatts. When peak masses happen, the storage system helps to scale back them. This “peak shaving” is changing into more and more vital on this period of upper electrical energy necessities on account of electromobility, warmth pumps and different electrical shoppers, as capped load peaks not solely cut back grid prices however ideally can even cut back the necessity for expanded upstream grids.
Quickly controllable power storage techniques such because the system on the Leipzig plant additionally play an vital position within the power market. The stationary battery storage system might be built-in into the balancing power market in each marketable type by the top of the 12 months — together with, along with peak shaving, as a grid stabiliser for the upstream distribution grids.
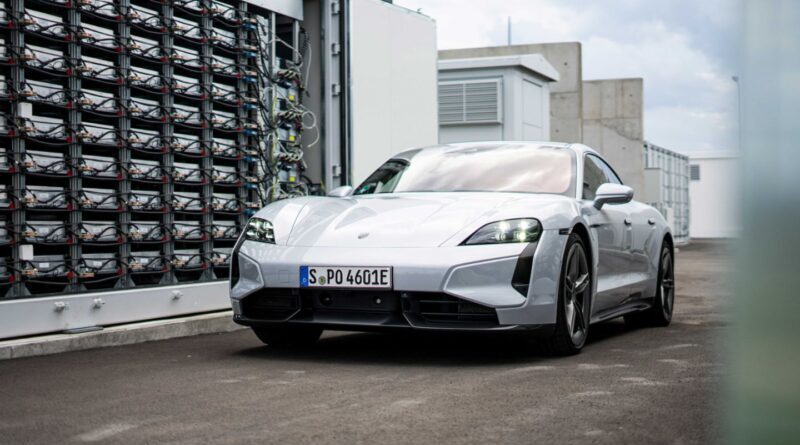
Porsche manufacturing — carbon-neutral and utilizing renewable power
Porsche manufacturing at its websites in Zuffenhausen, Leipzig and Weissach has been carbon-neutral since 2021. Since 2017, Porsche has been utilizing solely electrical energy from renewable power sources. The manufacturing websites in Stuttgart-Zuffenhausen and Leipzig, for instance, obtain their power from inexperienced electrical energy and biomethane. The Leipzig web site additionally obtains district heating from biomass.
Article by Porsche. Ekkehard Kleindienst, Spokesperson Manufacturing and Logistics.
Have a tip for CleanTechnica? Wish to promote? Wish to recommend a visitor for our CleanTech Discuss podcast? Contact us right here.
Newest CleanTechnica.TV Movies
CleanTechnica makes use of affiliate hyperlinks. See our coverage right here.
CleanTechnica’s Remark Coverage